As a high calorific value green and environmentally friendly clean energy source, hydrogen has become the choice of mainstream countries around the world to replace traditional fossil energy.
Currently, "steam methane reforming" is a mainstream hydrogen production scheme. Due to its abundant coal resources, China mainly uses coal to produce hydrogen.
However, both of the above hydrogen production schemes rely on the consumption of traditional fossil energy, and the production process also brings a large amount of carbon emissions.
Therefore, this is not an ideal hydrogen production scheme. The hydrogen prepared by the above scheme is called "grey hydrogen", and after an additional carbon capture step, "blue hydrogen" will be obtained.
A more promising hydrogen production scheme is to use electrical energy converted from renewable energy sources such as solar and wind energy to drive the catalyst electrode to crack water and produce hydrogen. This process does not produce any carbon emissions, and the obtained hydrogen is called "green hydrogen".Because the consumption of hydrogen gas (such as for fuel cells) only produces water as a byproduct, and water is also the raw material for green hydrogen production, it can be seen that green hydrogen is almost one of the most perfect substitutes for fossil energy.
Advertisement
However, the current production cost of green hydrogen is too high, almost 2 to 3 times or more than the price of grey hydrogen, which hinders the large-scale popularization of water electrolysis hydrogen production technology. At present, the hydrogen production brought by this technology only accounts for about 5% of the annual hydrogen production.
In the process of green hydrogen production, about 70% of the cost comes from the consumption of electrical energy. Therefore, an effective measure to reduce the production cost of green hydrogen is to develop high-performance water electrolysis catalysts to reduce the electrical energy required for the water electrolysis process.
In the industrial field, water electrolysis for hydrogen production is mainly carried out in alkaline water electrolyzers, which have the advantages of maturity and stability, and low construction cost. However, due to the low activity of the catalytic electrodes, the production cost of green hydrogen is relatively high.
In addition, in order to ensure a higher energy utilization efficiency, that is, to ensure the efficiency of converting electrical energy into hydrogen energy, it is often necessary to operate at a lower current density of 200mA/cm2-500mA/cm2.High-Performance, Low-Cost New Hydrogen Production Technology
Based on this, Dr. Yong Zuo, who is currently engaged in postdoctoral research at the Italian Research Institute, and his colleagues, on the basis of previous work [1], have developed a nanoscale Cu-Ru heterojunction catalyst that can greatly enhance the catalytic activity of the electrode.
In the study, the research team paired the Ru-Cu cathode with a stainless steel mesh anode, assembled in an alkaline electrolytic cell device, and then conducted accelerated pressure water splitting tests with intermittent power supply.
The results showed that the electrolytic cell was able to maintain good working performance, and there was no degradation even in long-term continuous testing.This indicates that the developed combination of anode and cathode in this study is expected to be used in alkaline electrolyzers powered by renewable energy sources such as solar energy, thereby facilitating the production of green hydrogen.
Figure | The performance of the Ru-Cu electrode as the cathode, paired with a stacked stainless steel anode, after assembly in a single cell of an alkaline electrolyzer (source: JACS).
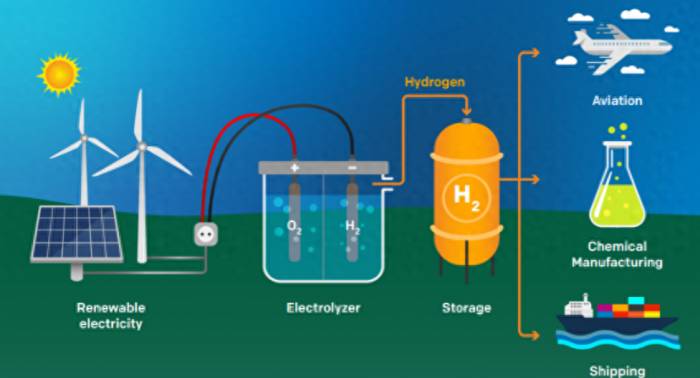
Currently, hydrogen production technology using alkaline electrolyzers is facing the bottleneck of high costs and low performance. The nanoheterostructure based on Ru-Cu developed in this study shows promising performance in the hydrogen evolution reaction while maintaining cost-effectiveness.
This is an important advancement in the development of platinum-free materials using the cathode of an alkaline water electrolyzer.From minimal experimental results to the completion of two consecutive papers
At the beginning of the research, they attempted to synthesize vertically grown Cu nanorod arrays on the surface of a copper mesh substrate, hoping to achieve a three-dimensional structure with a large surface area base.
However, the research team found that the precursor of these nanorod arrays would inevitably undergo severe collapse and detachment during the process of being reduced to Cu.
To address this, they also studied catalysts based on non-noble metals and are currently developing a simple method suitable for the industrial scale preparation of molybdenum sulfide-based cathode materials.
In addition, Zuo Yong and others have developed an electrochemical activation strategy that can significantly activate and continuously regenerate the oxygen evolution performance of commercial stainless steel mesh as the anode in alkaline water electrolysis cells.
The team believes that this is because the crystal structure difference between Cu and its precursor is too large, making it impossible to maintain the morphology during this transformation process.After a series of explorations, they found a thin-film coating method that can prevent the collapse of precursor nanorod arrays during the reduction process.
However, the research group invested more time in the synthesis and exploration of high-quality three-dimensional Cu substrates, thus completing the core part of this work.
During this period, they also studied the reasons why this catalyst has excellent electrocatalytic hydrogen production performance in an alkaline environment.
They found that there is a synergistic effect in the catalytic process of the Cu-Ru heterojunction. Specifically, the electronic structure of ruthenium is regulated by the size of the surface Cu clusters, which can promote the dissociation of water.
The Cu clusters grown on the surface of ruthenium show a change in the Gibbs free energy of hydrogen adsorption close to zero, which can promote the rapid production of hydrogen gas.Additionally, they paired it with commercial stainless steel (as the anode) to assemble an alkaline electrolysis cell with a single battery, and evaluated its performance under simulated industrial conditions.
It was found that under a high current scenario of 1A/cm2, after intermittent operation (simulating the scenario of hydrogen production powered by solar energy, etc.), or continuous operation for several hundred hours (simulating the scenario of grid-connected hydrogen production), this alkaline electrolysis cell showed good stability.
Further technical and economic analysis showed that after assembling it in a 1-megawatt water electrolysis plant, the unit price of hydrogen production reaches the international mainstream green hydrogen production price target (2-2.5 US dollars/kg). It also approaches the production price of coal-based hydrogen (for example, when the coal price is between 450-950 yuan/ton, the price of coal-based hydrogen is between 9.73-13.70 yuan/kg).
This proves that compared with the gray hydrogen production based on fossil fuels, this electrolysis water technology has a certain competitiveness.
It should be pointed out that the solution proposed this time depends on the use of ruthenium. Ruthenium is a precious metal and a by-product of platinum extraction, with only 30 tons obtained by humans each year. However, the cost of ruthenium is relatively low, with a market price of about 40% of platinum and 10% of iridium.Typical membrane electrolyzers, such as cation exchange membrane electrolyzers, require a significant amount of platinum (at the cathode), approximately 0.5g per kilowatt, and about 1g-2.5g of iridium (at the anode) per kilowatt.
In contrast, the technology developed in this study uses only about 0.04g of ruthenium per kilowatt, or just 0.052mg of ruthenium per square centimeter of electrode area.
Although the use of ruthenium increases the cost of the electrodes slightly, it greatly reduces operating costs. Therefore, the appropriate use of ruthenium in alkaline water electrolyzers is an effective solution to address the issues of poor working performance and high production costs of green hydrogen.
Recently, the related paper was published in JACS[2] with the title "Ru-Cu Nanoheterostructures for Efficient Hydrogen Evolution Reaction in Alkaline Water Electrolyzers."
Zuo Yong is the first author and co-corresponding author, while Sebastiano Bellani, a senior researcher at the Italian commercial company BeDimensional, and Professor Liberato Manna from the Italian Institute of Technology, serve as co-corresponding authors.Despite the reported Ru-Cu catalyst only requiring a small amount of Ru, the distribution of ruthenium will become a new issue due to the high dependence of other key technologies, such as fuel cells, on precious metals including ruthenium.
To address this, they also studied catalysts based on non-precious metals. Specifically, Zuo Yong and others have developed an electrochemical activation strategy that can activate and regenerate the oxygen evolution activity of commercial stainless steel mesh.
Recently, the relevant paper was published in Advanced Materials with the title "Stainless Steel Activation for Efficient Alkaline Oxygen Evolution in Advanced Electrolyzers."
Zuo Yong is the first author and co-corresponding author, while Sebastiano Bellani and Liberato Manna serve as co-corresponding authors.
In this Advanced Materials paper, they also explored the development of high-performance anodes based on non-precious metals.In general, the paper in Advanced Materials reports a simple voltage pulse strategy that can activate and rejuvenate the performance of an electrolytic cell equipped with a stainless steel anode.
Subsequently, the research group plans to use an industrially viable simple synthesis strategy to develop efficient catalytic electrodes with practical industrial applications.
And to test the authenticity of performance in a commercial pilot scale (kW) test, in order to better evaluate its prospects for use in industrial electrolytic cells (MW), and to promote the transformation of results and industrial application.
POST A COMMENT