Upon close examination, we can observe that many organisms in the natural world possess the ability to change their shape. Organisms of various sizes alter their forms to effectively survive and reproduce in complex natural environments.
For instance, armadillos curl their bodies into a ball to protect themselves from danger, while frilled-neck lizards display their umbrella-like neck flaps as a sign of threat and for mating. On a microscopic level, single-celled organisms like amoebas extend pseudopodia for movement and feeding, while planarians can contract their spasmoneme within milliseconds.
This shape-shifting is produced by a complex interplay of soft and rigid structures, characterized by excellent adaptability, flexibility, compliance, energy efficiency, and safety.
Drawing inspiration from nature's solutions can create artificial systems capable of transformation, with potential applications spanning robotics, wearable devices, materials science, and bioengineering.
Based on existing literature, there is currently no research on driving ultrafast micro-actuators for shape transformation using acoustic methods. Recently, PhD student Zhang Zhiyuan from the Swiss Federal Institute of Technology in Zurich and his team have achieved the design of variable micro-actuators using the powerful driving force of an acoustic field.Recently, a related paper was published in PNAS [1] with the title "SonoTransformers: Transformable Acoustically Activated Wireless Microscale Machines."
Advertisement
Zhang Zhiyuan is the first author of the paper, and Zhejiang University Ph.D. student Shi Zhan is the second author. Assistant Professor Daniel Ahmed from ETH Zurich served as the corresponding author.
The combination of sound waves and deformable materials has led to the creation of a new type of acoustic transformer.
Shape transformation in artificial systems is achieved through various driving methods, such as mechanical pushing, pressurized fluids, shape memory polymers and alloys, dielectric and liquid crystal elastomers. Researchers have also utilized a range of external stimuli and fields, including chemical gradients, light, heat, humidity, electric fields, and magnetic fields, to drive small, unbound machines.
However, most existing deformable machines are limited to centimeter or millimeter-sized structures, which hinders their use in miniaturized micromachines. These pioneering studies also exhibit certain limitations. For example, most driving methods are usually slow (1 to 150 seconds), resulting in low deformation speeds.Although electromagnetic actuation can be considered instantaneous, it requires complex pre-programming to produce micro-machines compatible with these methods, such as pre-designed magnetic moments, multi-layer structures, and multi-step processing procedures. More importantly, when scaled down, the underlying physical mechanisms that control their operation may be significantly affected or become ineffective.
When materials and structures are reduced to the micrometer scale, they often exhibit size-dependent characteristics, leading to unpredictable and uncontrollable mechanical changes during shape transformation.
In addition, surface forces such as van der Waals forces and electrostatic forces dominate at the microscale, leading to increased static friction and adhesion between tiny structures, making them more prone to breakage and more difficult to deform.
Acoustics offer a promising development path for deformable micro-machines, as they enable miniaturization at the micrometer and nanometer scales, simplified design and rapid prototyping, remote and wireless operation, and ultra-fast and reversible deformation in milliseconds.
Zhang Zhiyuan said, "This study proposes a new concept of acoustic waves and deformable materials. This novel idea will promote the emergence of new concepts, new ideas, and new applications in various fields such as material science, soft matter, smart metamaterials, robotics, flexible electronics, adaptive optics, micro-medicine, and micro-engineering."The acoustic micro-machine designed by the research group is named "SonoTransformers," which refers to a type of acoustically activated transformable micro-machine that utilizes pre-programmed soft hinges with varying stiffness to provide the capability for shape transformation.
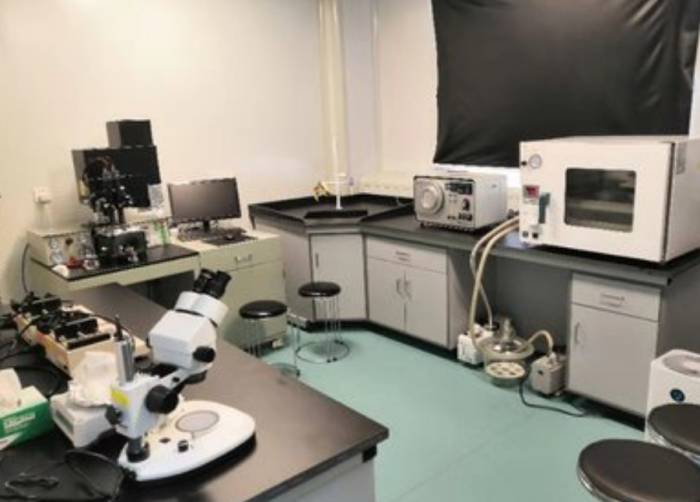
When exposed to an acoustic field, these soft hinges concentrate acoustic energy through enhanced vibration and provide the necessary force and torque for the entire micro-machine's deformation within a few milliseconds. Researchers have created a new machine design to pre-determine the folding state, thereby achieving precise programming and customization of acoustic deformation.
In addition, the study also demonstrated the ability to selectively drive the transformable micro-robots by adjusting the acoustic field power, ultimately achieving highly controlled and diverse functions.
The reviewers commented that this study is the first to propose the concept of acoustically variable micro-machines, and this acoustic activation mechanism provides a multifunctional platform for the study of micro-machines and micro-robots.Controllable Micro-Deformation: A Platform for Exploring the Interaction between Acoustics and Soft Materials
So, how are these acoustic micro-machines manufactured?
Zhang Zhiyuan said that they used a customized ultraviolet light polymerization technology to create a prototype of the acoustically deformable micro-machine. When ultraviolet light passes through the photomask, the design pattern of the micro-machine is projected onto a hydrogel mixture, causing the hydrogel mixture to polymerize. This method can produce up to 500 micro-machines in a single batch within 3 minutes.
To achieve different stiffness and thickness in the micro-machine, they designed a photomask with blank and grid elements. This design can change the local exposure intensity of the mixture. Blank elements will cause the hydrogel to fully polymerize, producing relatively hard areas; while grid elements achieve partial polymerization, producing relatively soft areas.
The next key step is to achieve controllable deformation. The key factor for this miniature machine to deform in an acoustic field lies in the different stiffness of the soft hinges and rigid connections in its acoustically deformable micro-beam components.Using a high-speed microscope, the dynamics of deformable micro-beams in the sound field can be observed. Zhang Zhiyuan discovered an interesting phenomenon during observation: when the micro-beam is clamped at both ends and subjected to the action of the sound field, the soft hinge part exhibits a larger amplitude of periodic oscillation, indicating that the sound field is concentrated in the soft hinge area.
Through a series of characterization experiments on the length, width, and exposure time of the soft hinge, researchers found that thinner, longer, and softer soft hinges lead to relatively lower rigidity of the micro-machine. Therefore, the soft hinge can easily generate greater sound force, resulting in more obvious folding. The programmability and selectivity of soft hinge acoustic activation provide more possibilities for the design of deformable micro-machines and micro-robots.
To control the deformation of the micro-machine, Zhang Zhiyuan designed various types of acoustically deformable micro-beams, such as micro-beams with straight, curved, and wedge-shaped soft hinges.
When driven acoustically, micro-machines containing these different soft hinges exhibit different behaviors. Specifically, the four-grid micro-machine composed of straight micro-beams contracts when sound-activated; in contrast, the micro-machine composed of curved micro-beams expands when stimulated by sound; micro-machines containing both straight and curved micro-beams fold and expand simultaneously. The use of different combinations of micro-beams allows for a variety of designs for acoustically deformable micro-machines.
"By effectively designing micro-machines, they can exhibit predictable and targeted deformation behavior," said Zhang Zhiyuan.Based on the deformable acoustic micro-beam, the team developed a quadruped micro-robot, the four square legs of which utilized soft hinges of varying lengths. By adjusting the acoustic excitation voltage, the square legs of the robot can selectively deform.
For excitation voltages below 30VPP, the micro-robot maintains its original shape. At 40VPP, the leg with the longest hinge folds. As the voltage further increases to 45VPP, leg 2 folds while leg 1 remains folded. Finally, when the voltage reaches approximately 50VPP, leg 3 folds along with the folded legs 1 and 2.
This adjustability enables addressable and programmable shape transformations, highlighting the potential of using acoustically deformable micro-beams to develop complex and multifunctional micro-robots.
Currently, acoustically activated deformable micro-machines only have in-plane 2D deformation capabilities. By introducing more complex structural designs and more powerful acoustic field excitation, acoustically deformable micro-machines will be capable of achieving torsion and folding in three-dimensional space.
The development of multifunctional acoustically deformable micro-beams and micro-machines paves the way for progress in multiple scientific fields. From a physics perspective, it provides a new opportunity to explore the interaction between acoustics and soft matter, such as vibration modes and synchronization effects.In the field of metamaterials, the integration of acoustically deformable micro-beams aids in the transformation of complex 3D shapes and the creation of 2D to 3D origami/kirigami microstructures. These structures can be used for optical guidance, acoustic guidance, and energy amplification.
In the realm of robotics, acoustically deformable beams have opened up a novel paradigm for microscale design, enhancing maneuverability by enabling functions such as steering, propulsion, and environmental adaptation.
For the medical field, these micro-robots are expected to dynamically navigate through complex blood vessels in the near future, as acoustic fields can easily penetrate the body.
Overall, the research proposes a brand-new paradigm for the design of acoustically driven soft robots, which is achieved by utilizing a network of soft hinges with varying stiffness to realize the deformation, motion, and other functions of soft robots. Acoustically driven soft robots represent a new yet rapidly developing field, and the research team will design more novel soft robots based on the soft hinge design.
POST A COMMENT